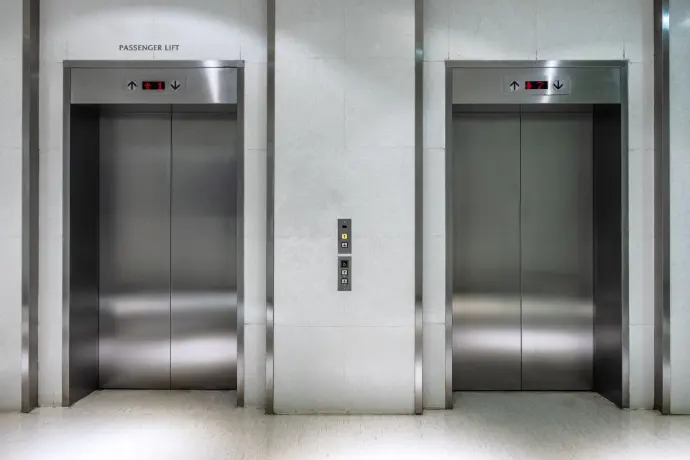
Stainless steel, as we know, is one of the main materials used in industry in general thanks to its properties, which include its aesthetics, in addition to its structural and inherently stainless properties. Furthermore, or due to these same properties, it is a material that does not require coatings, so its final finish will be the same material.
Among the options available for bonding it, the traditional ones, as we already know, are rivets, which deteriorate its aesthetics, and welding, which also have some adverse factors, such as marks that can perforate the sheet if the gauges are very thin.
Welding Stainless Steel
While it is the most suitable method for joining metals, welding stainless steel presents several technical challenges due to differences in the physical and chemical properties of the materials.
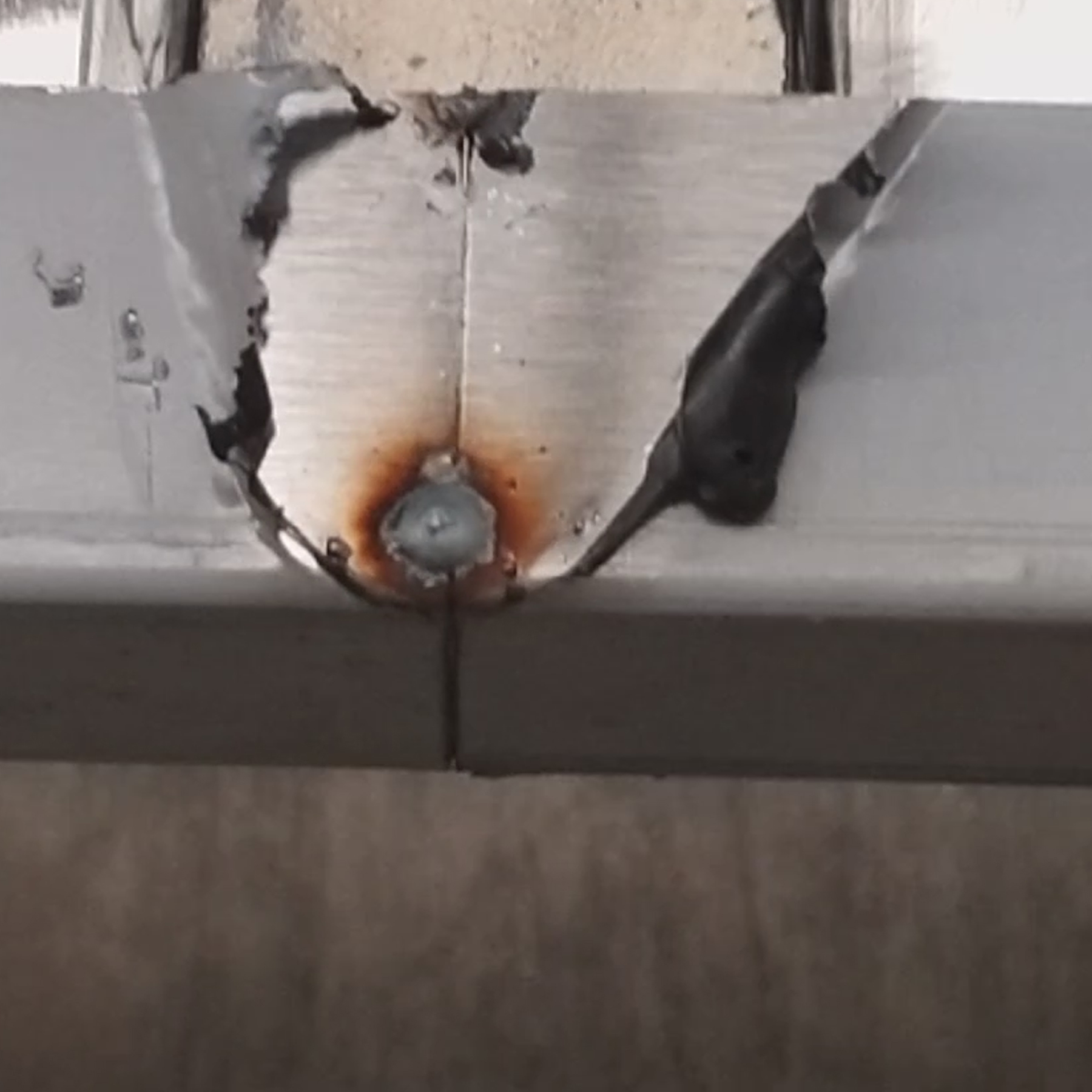
Chemical differences: Stainless steel contains chromium, which gives it corrosion resistance, while other alloys may not have this characteristic.
Uneven thermal expansion: Stainless steel and other alloys have different coefficients of thermal expansion. This can cause internal stresses and deformations in the weld.
Cross-contamination: Stainless steel is very sensitive to contamination by iron particles or other metals, which can compromise its corrosion resistance.
Consumable selection: It is crucial to choose electrodes and welding wires compatible with both materials to avoid welding defects.
Oxidation: During welding, stainless steel can develop an oxide layer that affects both its aesthetics and corrosion resistance.
Stainless Steel Riveting
Using rivets as an alternative to joining stainless steel with other materials could be an option, but it can also present several challenges, mainly due to galvanic corrosion.
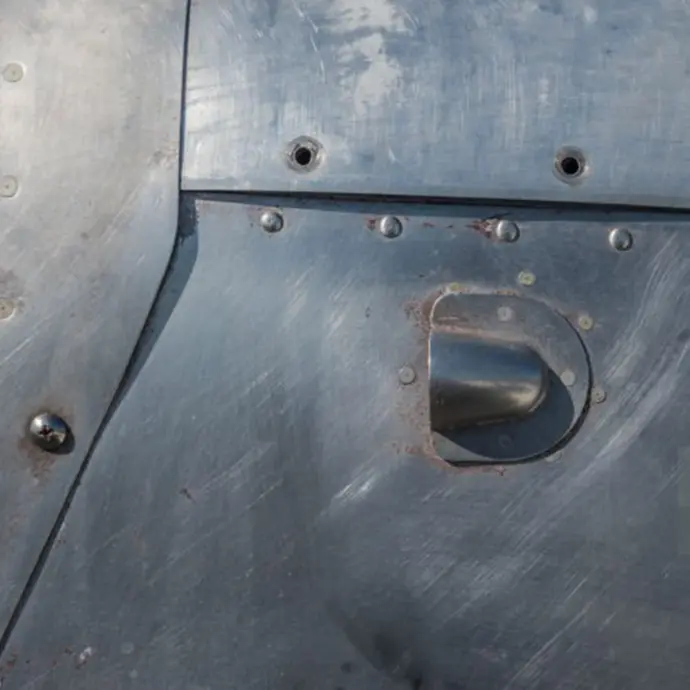
Galvanic corrosion: Stainless steel is more noble than other steel alloys, which means that when combined in the presence of an electrolyte, the less noble material will corrode faster. This can weaken the bond and reduce the service life of the structure.
Differences in thermal expansion: Stainless steel and other steel alloys can have different coefficients of thermal expansion. This can generate stresses in the riveted joint when temperature changes occur, leading to fatigue and possible structural failure.
Mechanical failures: Rivets can fail due to excessive loading, fatigue or poor installation. If rivets are not designed to withstand the forces applied, they may loosen or break over time.
Contamination of stainless steel: If carbon steel or aluminum rivets are used, they can contaminate stainless steel, accelerating corrosion and affecting its appearance and strength.
MMA Structural Adhesives
While welding and rivets remain the traditional method for joining stainless steel, Methyl Methacrylate (MMA) structural adhesives provide a high-performance alternative that eliminates many of the challenges associated with welding.
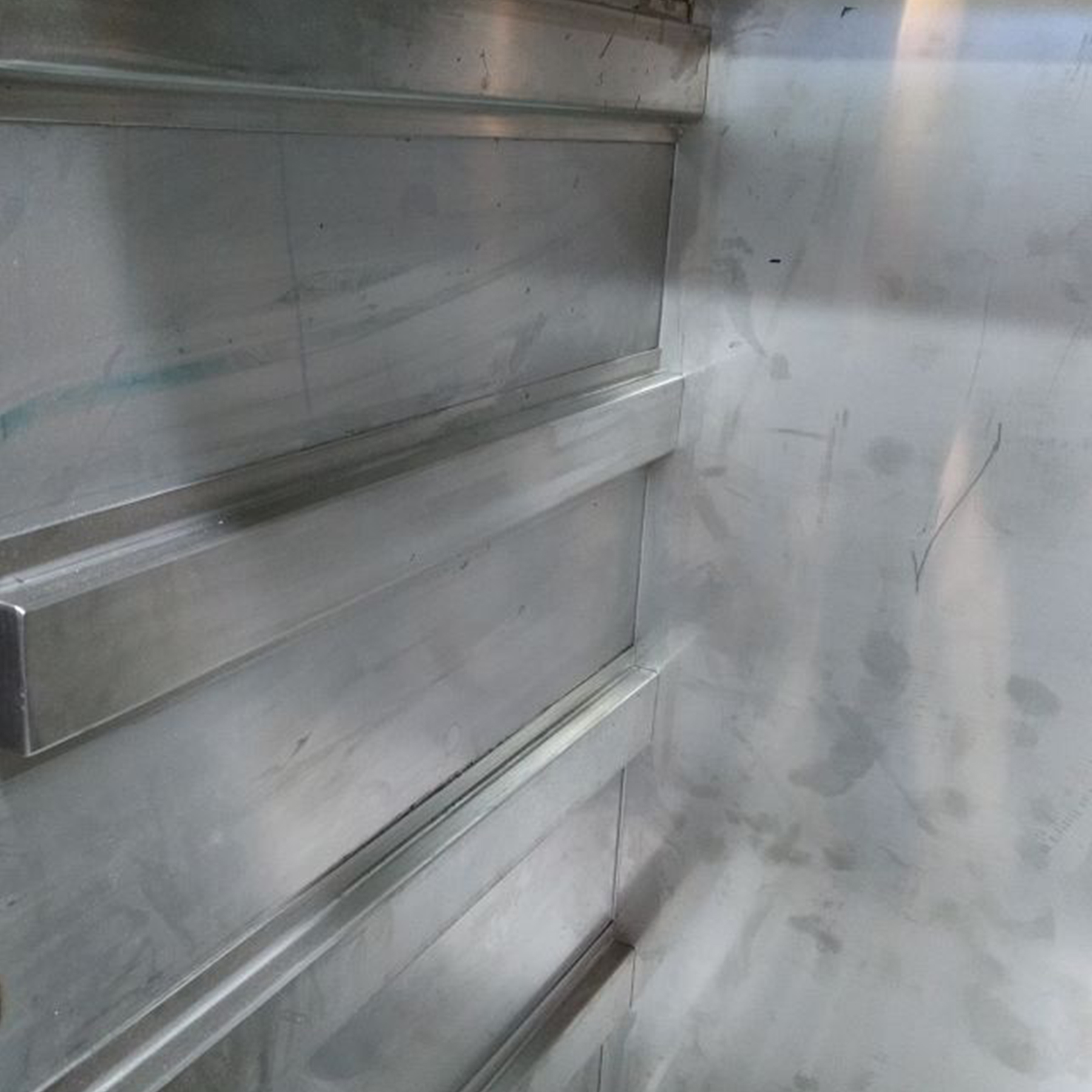
Prevention of galvanic corrosion: Acting as an insulating barrier between metals, MMA adhesives prevent ion transfer and minimize oxidation.
No need for heat or perforations: Eliminating risks of thermal deformation and stress concentration.
Uniform load distribution: Unlike rivets and bolts, which create localized stress points, adhesives distribute loads evenly across the bonded surface.
High resistance to vibration and fatigue: Structural adhesives absorb impact and cyclic loads more effectively, increasing joint longevity.
Easy application: MMA adhesives can be dispensed with an applicator gun, allowing for adjustments during the open time before curing.
Curing and Performance
MMA adhesives offer an optimized curing process for industrial applications:
Full curing:
Afterward, wait 24 hours for the adhesive to reach 100% of its capacity, after which its curing time is complete.
Open time:
In the first 4 to 6 minutes, the adhesive can be moved or removed without causing damage.
Working time:
During this phase, it is not possible to move the substrates because the adhesive bonds are still very weak, and moving them can break them.
ADINOX M422, Gray Methacrylate Adhesive
ADINOX M422 is a high-performance methyl methacrylate (MMA) adhesive specifically designed for structural bonding of stainless steel:
- High-strength, flexible bonding without the need for heat.
- Corrosion resistance, preventing oxidation at the joint.
- Simple application with minimal surface preparation.
Conclusion
Stainless steel joining is a technically demanding process that requires careful material selection, heat control, and corrosion prevention measures. While traditional welding and riveting methods are still widely used, MMA structural adhesives offer an innovative alternative that eliminates heat-related defects, galvanic corrosion risks, and high manufacturing costs.